3次元フロービンシステム
高品質・高効率・フレキシビリティを実現!
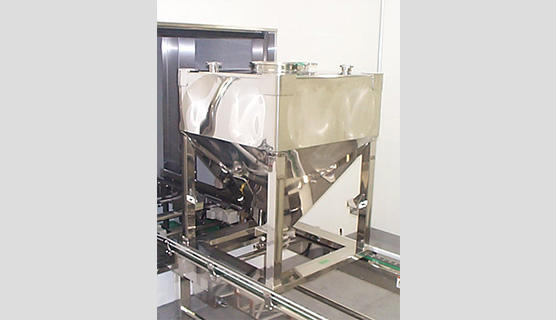
お困りごと
原料や中間製品を人や無人搬送車で搬送する従来の方法は、動線の複雑化や搬送リードタイムのロス、搬送用通路が必要なため敷地を広く確保しなくてはいけないなどの問題がある。作業負荷も軽減できてより効率的かつ安定して中間製品を搬送できる方法はないだろうか。
3大メリットを実現した「3次元フロービンシステム」
従来の人の手による搬送やAGV(無人搬送車)には、以下のような改善の余地がありました。
- 1人と物の動線の交差
- 2ヒューマンエラーの可能性
- 3搬送にかかるロスタイム、スペースのムダ
- 4上下に搬送するためには各工程で必要な箇所に昇降機能を取り付ける必要性
など。
開発の背景
製薬会社様と大成建設との新工場建設に向けた打ち合わせの中で構想が生まれました。既に物流倉庫などで導入されていたスタッカークレーンによる自動搬送システムを医薬品製造施設に応用できないか、と検討され、具現化に向けたプロジェクトが動き出しました。
医薬品製造施設はますます高品質化・高効率化・フレキシビリティを実現できる施設づくりが求められており、お客様のニーズと大成建設の技術開発案が融合して「3次元フロービンシステム」が誕生しました。
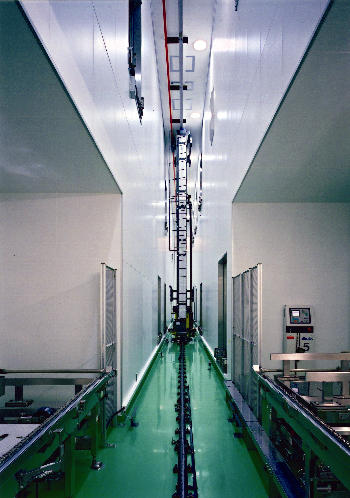
導入のメリット
高品質化を実現
- 搬送専用通路の設置により、人・物の動線を完全分離
- ヒューマンエラーの防止
- 製品を安定供給
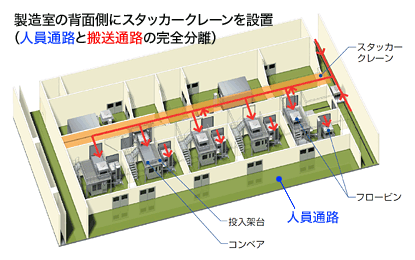
高効率化を実現
- 上下搬送をスタッカークレーンに集約
- 搬送リードタイムを短縮(従来比1/4に短縮)
- 搬送通路床面積を縮小(従来比1/3に縮小)
- 中間製品重量物搬送の作業負荷を軽減
フレキシビリティを実現
- 将来レイアウト変更が可能な柔軟性
- 上下搬送により生産機器への供給高さの自由設定が可能
更に、
フロービンを採用することによるメリット
- 混合機の切替時間を短縮
- 中間製品の保管
- 洗浄切替の効率化
- バッチサイズの大型化
- バッチサイズの大型化
が挙げられます。
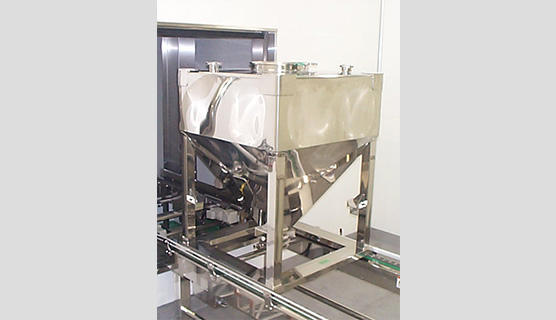
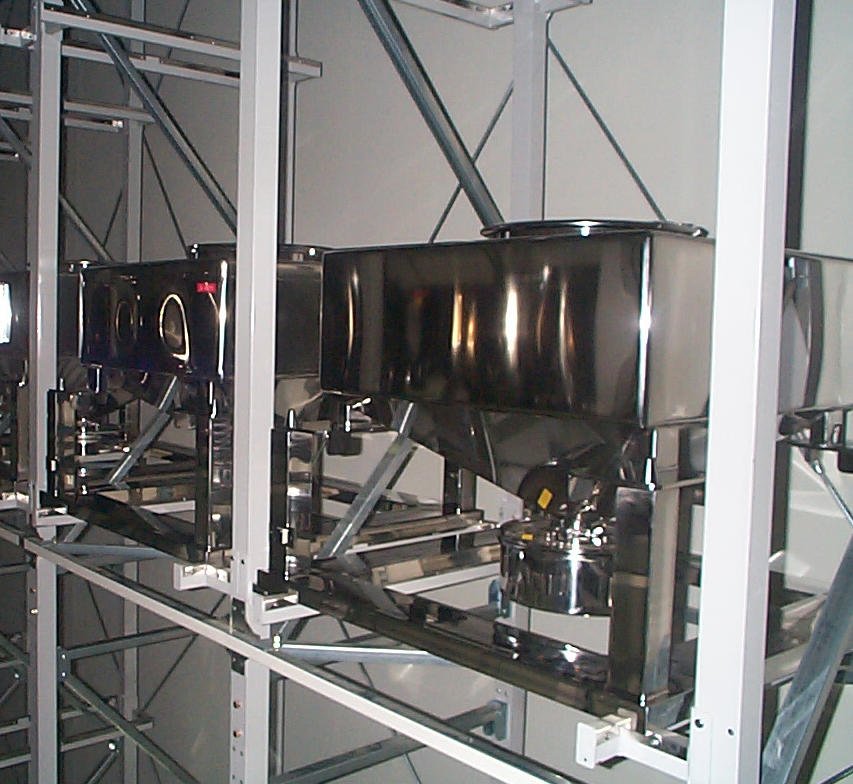
主な採用事例
当初はシステムの全てが自動であることに対して懸念する声もありましたが、システムの安定性や安全性、効率性などが実証され、お客様に理解されていくにつれて採用実績も増え、今では医薬品業界における主流な技術の一つとなっています。
スタッカークレーン方式の採用事例
竣工 | |
---|---|
明治製菓株式会社(現 Meiji Seikaファルマ株式会社) | 2004年3月 |
杏林製薬株式会社様 能代工場新製剤棟 | 2006年3月 |
大洋薬品工業株式会社様 高山工場第三製剤棟 | 2007年7月 |
塩野義製薬株式会社様 摂津工場固形製剤包装棟 | 2008年11月 |
株式会社廣貫堂様 呉羽工場固形製剤棟 | 2010年4月 |
小林化工株式会社 清間第一工場 | 2011年6月 |