省エネ・CO2削減にも対応したクリーンな工場をつくりたい
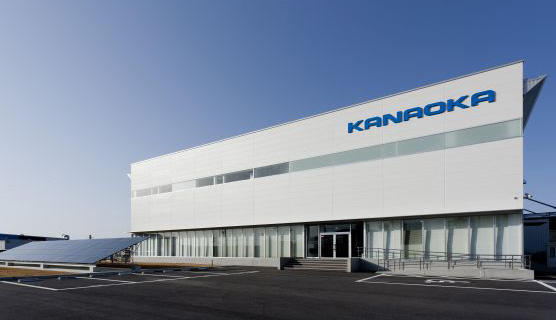
お困りごと
既存の大阪工場と名古屋工場を統合して新工場をつくり、西日本の拠点として運用していきたい。高度なクリーン工場であることはもちろん、環境に配慮し、省エネ・CO2削減に対応する新工場をつくりたい。
成功事例
軟包材業界のトップランナー企業として、食品や衛生用品など幅広い製品分野の包装材を提供する株式会社カナオカ様。
1951年の創業以来「お客様第一」の姿勢を貫き、「包装もまた商品の一部である」という考えのもと、清潔・安全性、デザイン性などの付加価値をもつ高品質なパッケージ商品を提供されています。
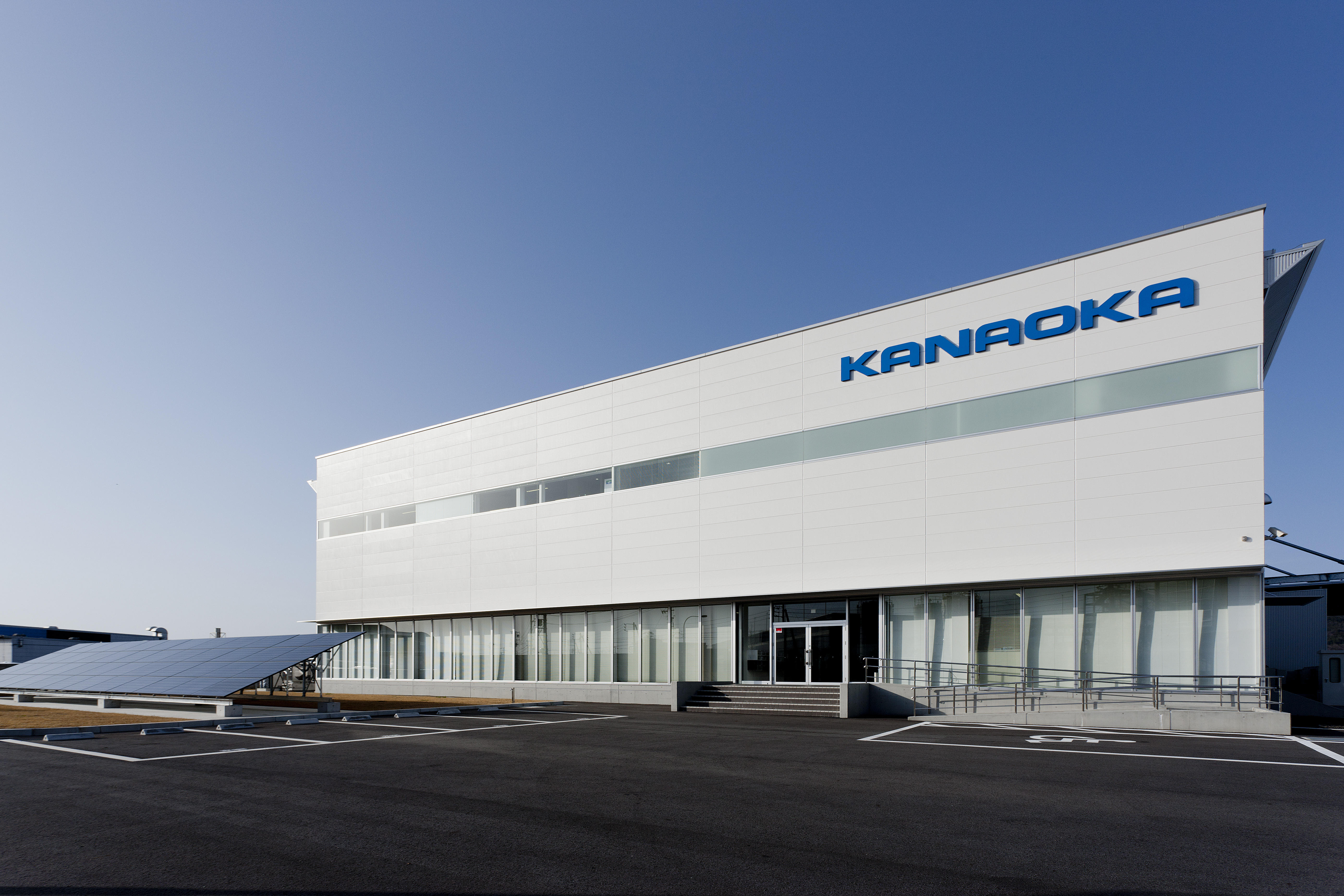
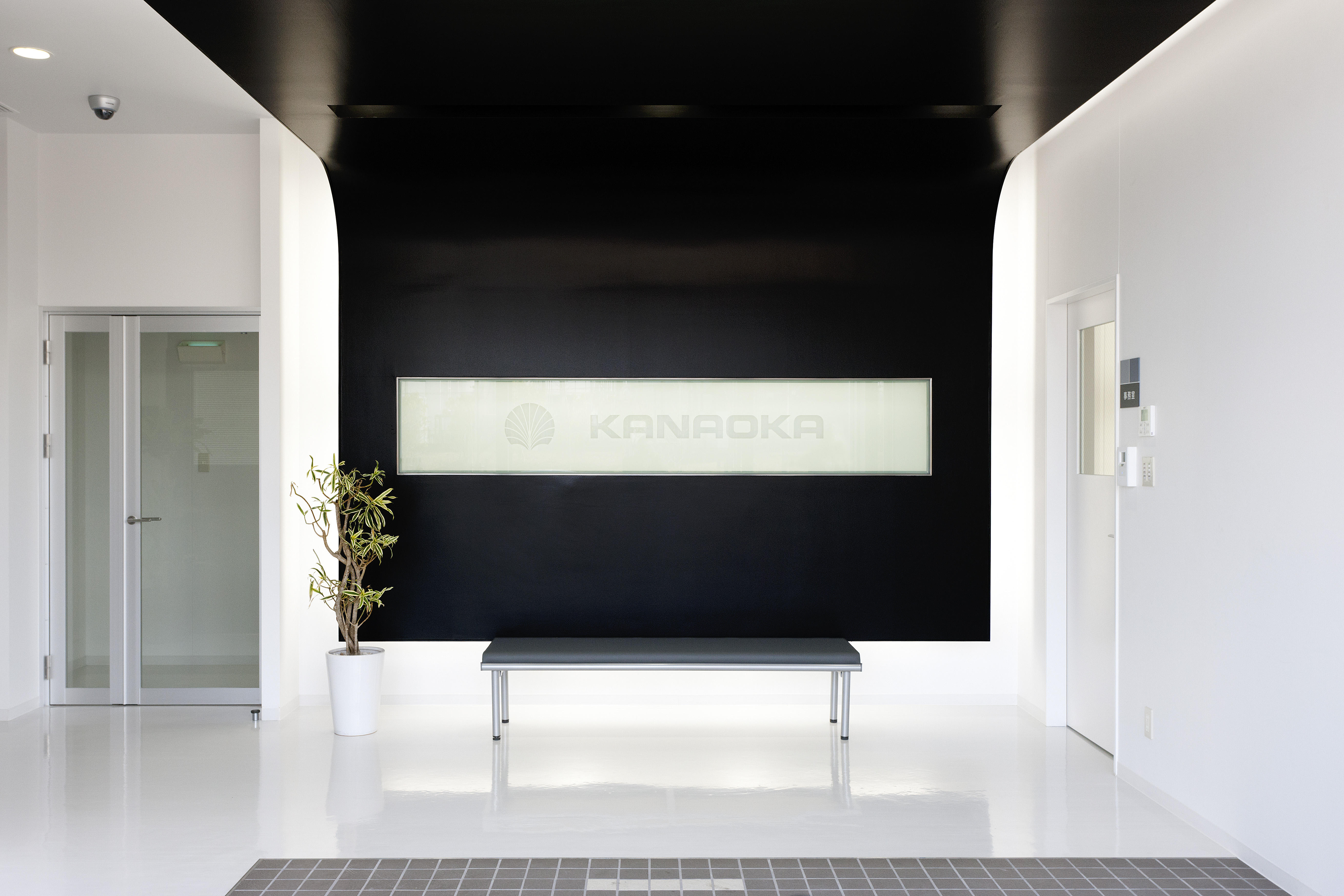
三重県伊賀市に新設された関西工場は、2011年6月に大成建設の設計・施工により完成しました。「コンパクト&エコな工場」をコンセプトに計画された新工場では、CO2の年間排出想定量を約30%削減するなどの効果が見込めます。
ソリューション1:明確なゾーニングで作業効率をアップ
新工場の南側を一般ゾーン、中央を生産ゾーンとし、将来の増設対応を考慮して北側に倉庫ゾーンを設けることで明確なゾーニング構成としました。
人とモノがスムーズに流れるよう、材料や中間製品をまとめて保管・管理する自動倉庫と、印刷室や加工室など各作業室を機能的に配置しました。ムダのない動線計画を行うことで作業効率アップを図りました。
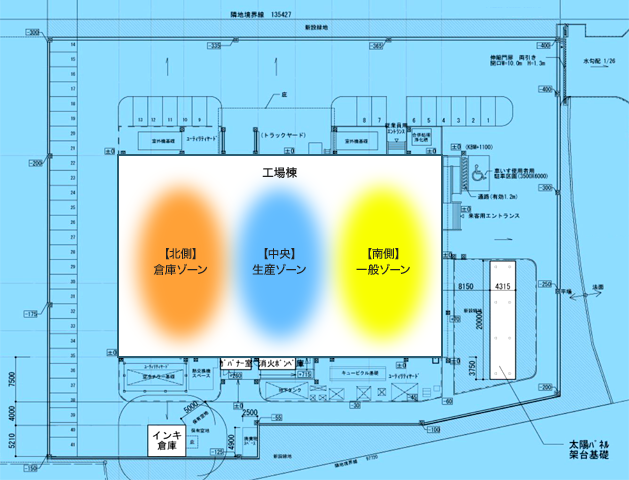
ソリューション2:衛生環境を強化し、クリーンな工場を実現
従業員用の入口・通路と来客者用の入口・通路を分けて設置
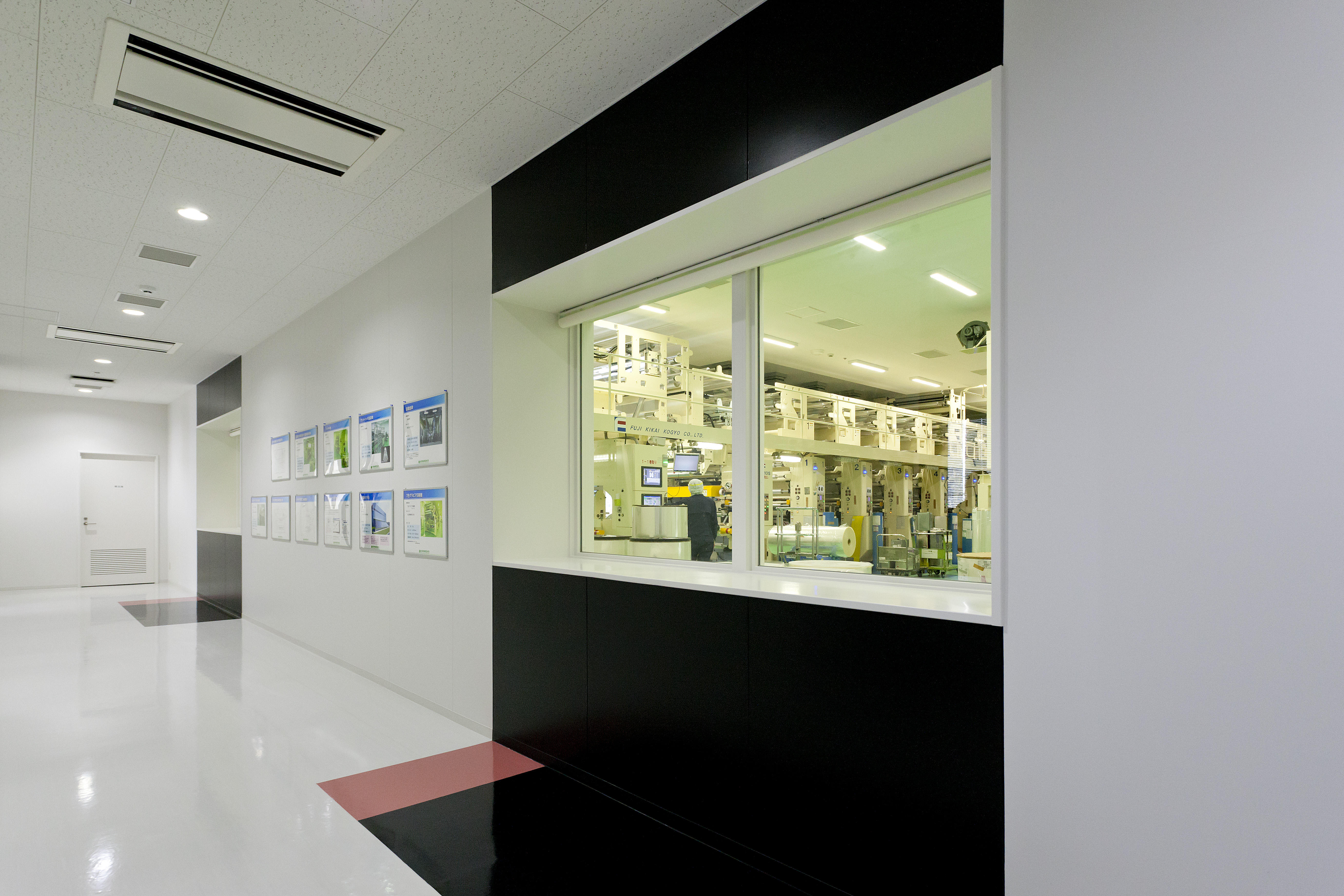
生産エリアへは従業員用の通路からのみ入室することができます。従業員用の通路は、2階に設置された1次更衣室、2次更衣室、エアシャワーを完備したサニタリーゾーンへとつながっています。
2次更衣室では、室内履きを生産エリア専用のものへと履きかえ、塵の除去や手洗い、エアシャワーを浴びるなど徹底的にクリーンな状態にしてからでなければ1階の製造エリアに入れないよう徹底管理しています。
一方、お客様は来客者用の入口から入り、1階に設けた見学通路から生産エリア内を見学することができます。
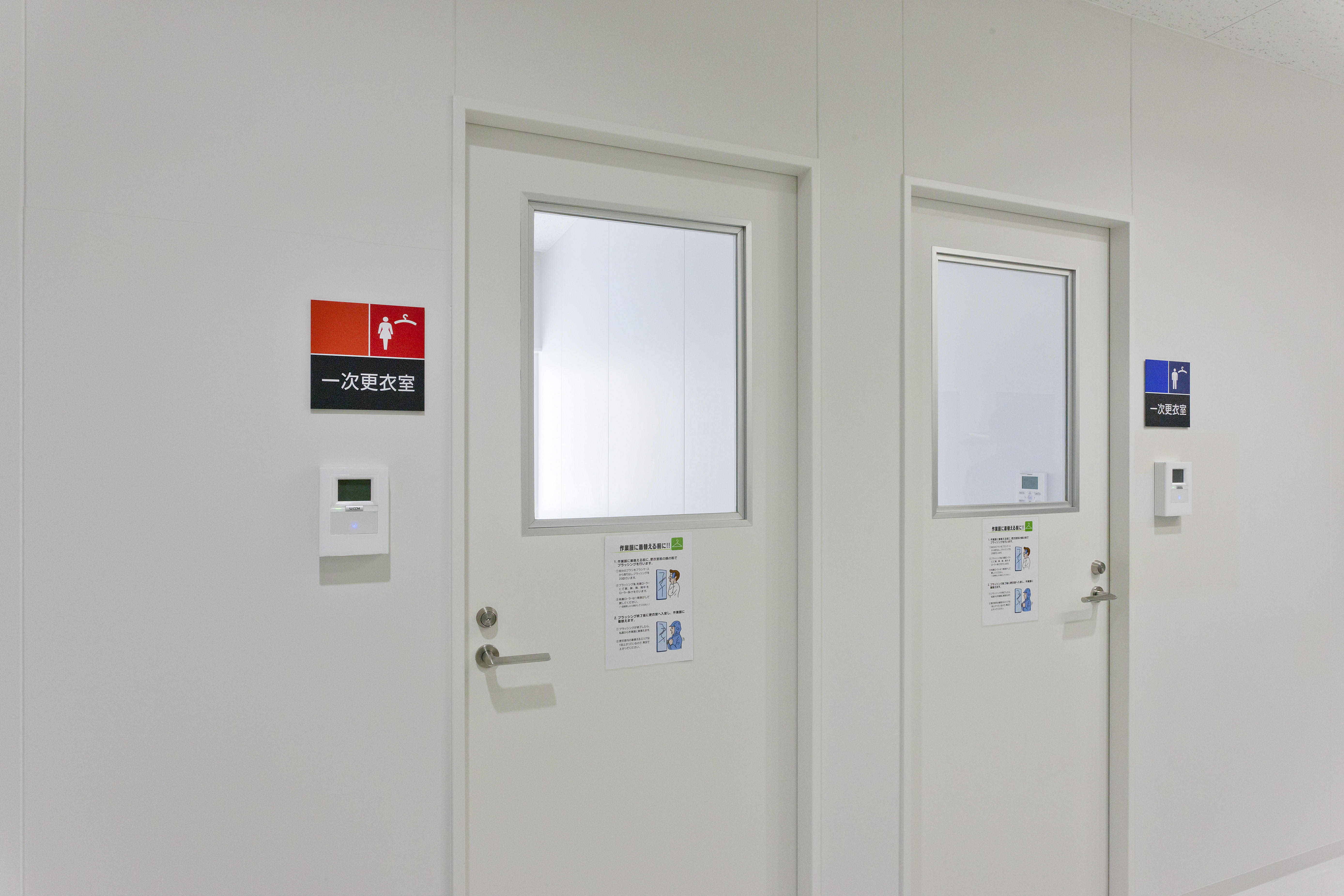
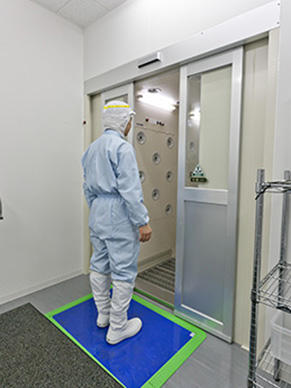
自動倉庫の導入により、省スペース・省エネ・省人化を実現
お客様からの急な発注にも対応する体制を整えるため、自動倉庫を導入しました。自動倉庫にはおよそ40,000アイテム分の材料を常時保管しており、各材料を保管するすべてのパレットをバーコード管理することで、材料の入出荷情報を迅速かつ的確に把握しています。
また、自動倉庫と生産エリアを隣接させ、材料などを出し入れする際の動線を短くコンパクトにすることで、作業効率を上げるだけでなく省スペース・省エネ・省人化を実現しました。
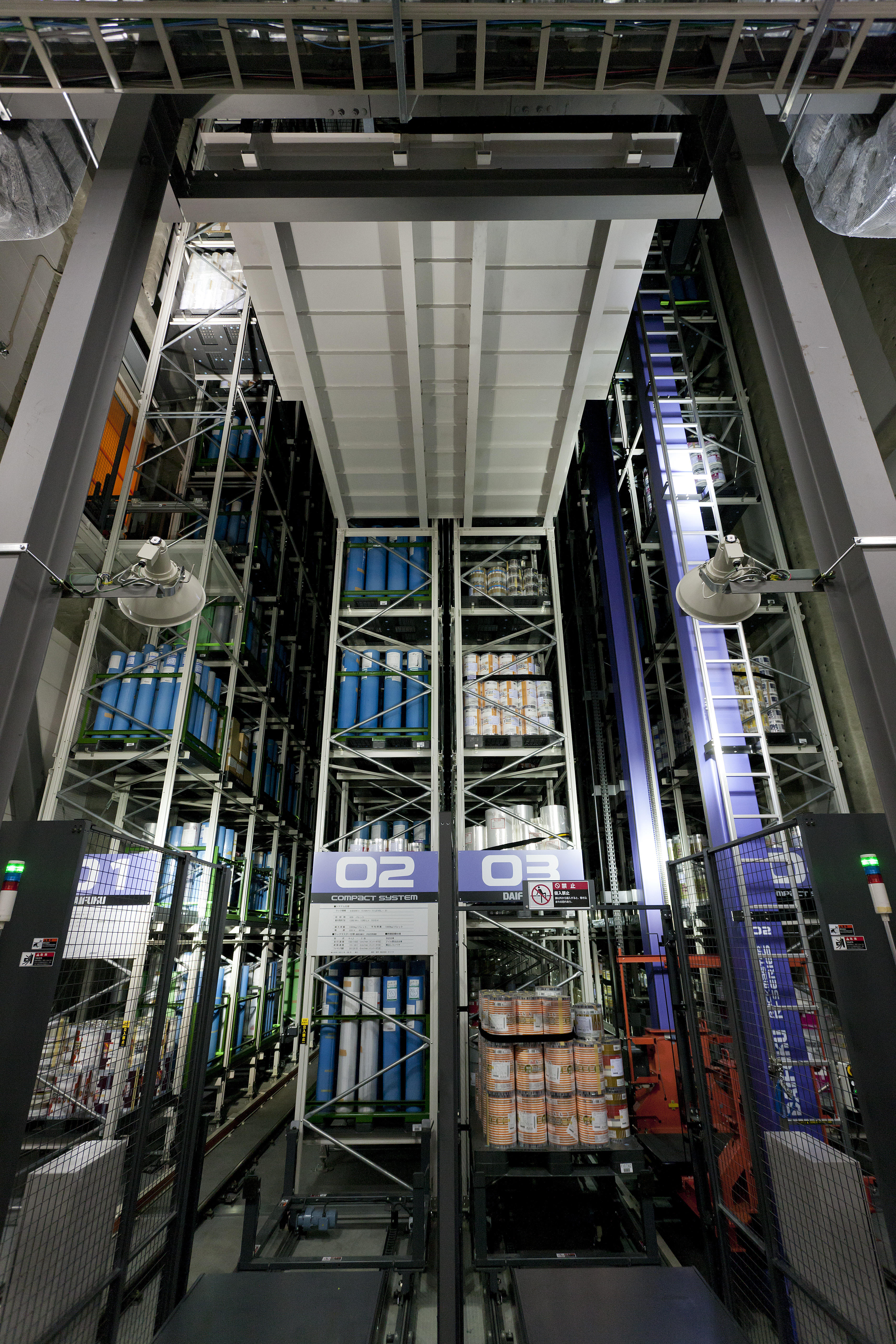
株式会社カナオカ 関西工場 工場長 板垣 芳行 様
自動倉庫ではバーコード管理を徹底することで、材料の入出荷情報を的確に把握しています。ヒューマンエラーの心配も要りません。必要なものがどこにあるのか、すぐに分かるため、管理がしやすく作業効率も向上しました。
株式会社カナオカ 関西工場 工場長 板垣 芳行 様
私たちの業務では、自動倉庫と印刷室、加工室、入出荷エリアなどのあいだでモノの出し入れを頻繁に行います。関西工場では、各工程における人とモノの動きをよく考慮したゾーニングが実現されており、非常に効率よく働ける環境が整いました。